Production Reporting (Finished Goods Receipts)
Production Reporting (Finished Goods Receipts) as part of production processes in manufacturing industry, we follow multiple steps to achieve it. When we say, Finished Goods Receipts, its not just the FG alone, it could be Work In Progress (WIP), Configured Product, Assembly etc. These are part of production operations.
In Factory, we use the Raw materials to convert to Finished Goods or Semi Finished Goods based on the demands. We use Resources like Machine, Men and other overheads to produce. We measure production efficiency with key performance indicators those are in line with our business objectives. So the real time cost of the Finished Goods consists of multiple factors like
- Raw Materials costs accumulated as part of production process
- Consumables like Greece, Oil etc need for production operations.
- Electricity or Cost of OIL / Diesel on production floor
- Labor costs with real time monitoring of production activities and production rates
- Machines or equipment used
- Overheads like Management salary, Factory rent etc
- Other Costs like costs of a Production reporting tools thats used for real-time production monitoring purpose.
All the above are added to form the COST for ONE PROCESS at ONE STAGE as part of production activities by a production report process. manufacturing operation helps. As the RM converts to Work In progress (WIP1) stage, input cost is the total of RM and LABOR costs. As part of this, we follow Activity Based Costing approach (ABC), that helps to add the Raw Materials, Labor, Machines and Overhead costs to Finished Goods cost.
We use this menu to report Work In progress items (WIP) or Finished Goods (FG).
How to manage the Finished Goods Receipts / Production Reporting in ACTouch?
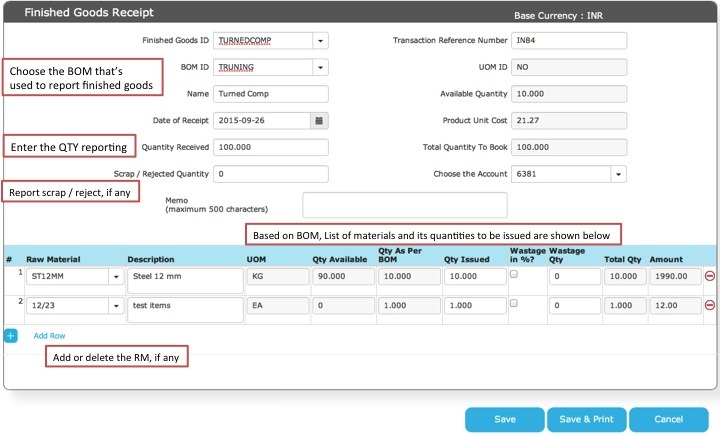
In ACTouch, you can do the following in FGR where you convert Raw Material to Finished Goods.
- Select a Finished goods ID from the drop down.
- Select a BOM ID – You can select any Bill of Materials which is used to report FG or WIP.
- Choose the date of FGR
- Enter FG / WIP quantity received – Based on this quantity and BOM, list of the raw materials will be shown with the quantity to consume.
- Enter reject quantity, if any
- We can see the product unit costs and costs that are shared between FG or by product, if any
- Select “Save” or “Save and print”.
Refer to the attached video for more details. Here we do the following as Production Reporting / Finished Goods Receipt is just a small portion of the entire workflows.
- Create a Sales Order for a Finished Goods.
- Covert it into a Work Order
- Report Production as part of the Reporting.
More information, click here
- Check here the ACTouch’s ERP Features
- How to implement an ERP Software that’s easy and quick to do?
- Problems that are faced by an ERP implementation
For a FREE ERP demo, send an email to sales@actouch.com
|