What is Material Requirements Planning (MRP)?
What is Material Requirements Planning or MRP?
We frequently hear this word in Manufacturing companies or CEO of a trading company is worried about materials movement, cost of inventory and how its managed etc. So Material Requirements Planning (MRP) / Materials Requirement Planning balances supply and demand for purchased and manufactured items. Given a set of demands or requirements, MRP automatically calculates a time-phased schedule of planned supply orders or adding the stock back to satisfy those demands.
Material Requirements Planning (MRP) looks at demand for finished items (Sales items) and uses product structure information / Bill of Materials (BOM) to calculate demand for Components / Raw materials.
For each item in the BOM, Materials Requirements Planning (MRP) looks at the ordering information, the Quantity currently on hand (in stock) and lead time to procure or manufacture (time to purchase or manufacture), and generates planned orders suggesting how many of that item to buy or make and when to do so.
Input for MRP is Master schedule or Forecast Demand or sales forecasts to arrive at total demand for a timeline and it plans to get to the bottom of BOM to Raw Materials level to check the demand. In case of multiple manufacturing process, if gets into Work In Progress items too. It checks the BOM for each production process and its Dependent demand items (WIP items) based on customer demands.
Its advantageous when we have a tight supply chain managementwith inventory costs to focus more. Having a definite customer lead times to delver, a tight production deadlines will make it sometimes challenging to Production team to meet production lead time and production deadlines, if there is a production delays due to unavoidable reasons.
So its essential to plan even production cycle process with a clear production process with a timeline and a buffer time too. Multi-level BOMs with a clearly indentified production capacity will add a control into capacity planning. Traditionally based on MRP inputs, the machine capacity planning is done.
MRP is good for discrete manufacturing, process manufacturing and project based manufacturing business companies. Once a Raw Materials list is done, purchasing activities begins, few times, inventory management depends on vendors Delivery schedules. In these types, it’s better to do material planning with a focus on Manufacturing businesses and its internal process, tools availability etc.
It takes demand from sources such as current and forecast orders, work orders, and parts below safety levels, subtracts supply, in the form of inventory on hand, on order, or in process, and calculates requirements for ordering or building parts to cover that demand.
Demand generated | Supply | Output |
Confirmed Sales Orders with Due date to delivery the items | Purchase Orders with Due date of delivery | Planned Purchase Indents |
Forecast | Confirmed Work Orders with Delivery date to deliver | Planned Work Orders with dates to deliver. |
Stocks that have gone below “REORDER Level” | Net quantity on hand (QOH) / Minimum Ordered Qty. | |
Planned Work Order that’s created manually. | ||
Master production schedule (MPS) |
There are few cases, where Manufacturing Resource Planning is also defined and considered for manufacturing process based on inventory requirements, Sales forecasts with Scheduling Production with machines and work process. Master production schedule from customer can be used as an inputs.
In manufacturing sector, Material requirements planning systems normally handles the need of material planning and future demand based on Sales Forecasts, Products Shelf life with demand-driven planning and demand for products.
ACTouch has many functionalities that are integrated with Material Requirements Planning (MRP) and its 100% compliant of a MRP System. For examples Sales, Purchase, Manufacturing, Purchase Indents, Inventory Controls etc.
Planning modules contains many features that’s explained below now.
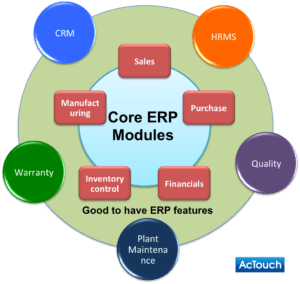
Material Requirements Planning (MRP) is a key manufacturing planning process that uses all sources of demand and supply to:
- Calculate gross item requirements and projected on-hand inventory
- Schedule and plan orders
Running an Material Requirements Planning (MRP) for production
There are two modes of MRP
- Regenerative MRP – plans for all items at selected sites. It recalculates demand and plans supply for all items. The first time you run MRP, it should be Regenerative MRP.
- Selective MRP– Prepare the plans only for items that have been selected. Typically this is run when the planning wants to be done specific to an item. In the business, the planning department has already run the demand for all the items and planning of RM and Finished goods are issued. But there is a sudden demand for an ITEM and need to replan. In this case, we do not want to affect the released plans and just plan the new items.
|
Types of Data considered for Materials Requirements Planning (MRP) or MRP Module
Need to capture the below items based on which the ORDER due date is calculated. To effectively run Material Requirements Planning (MRP) / MRP modules certain information relating to parts should be established. Since Material Requirements Planning (MRP) calculates the quantities to purchase or make based on this data, it is important to ensure that these parameters are maintained properly.
No |
Parameters |
Description |
1 | Location | Where this item is stored?
Typically in factories or warehouse, we store the materials in Racks, Floor etc. If a location is considered as a “SCRAP”, then the items in this location shouldn’t be considered. |
2 | Purchase / MFG / Configuration (P/ M / C) | Planning (MRP) uses the Purchase / Manufacturing code to distinguish manufactured items from purchased items. This is important for MRP to raise a Work Order or a Purchase Indents. |
3 | MRP Required? | Whenever the stock goes below REORDER level, we are generating the ALERTS on dashboard. |
4 | EOQ or Economic Order Quantity | This is the minimum quantity for which MRP will plan an order. If MRP determines that there is a need for a quantity of 22.5KG for a part, but that part has an EOQ of 50KG then MRP will recommend that an order for 50 is created.
This is only for Purchase type of Items (P) and not for anything else. |
5 | Order Quantity in multiples of | When the Purchase Indent is raised, it would be in multiples of this. This allows you to create orders in even multiples. As an example, if MRP determined there was a need for a quantity of 135 KG for a part, and the multiples was set to 50, MRP would create a planned order for 150, which is the next highest even multiple to cover the requirements. |
6 | Shrinkage / Loss Factor / Scrap % | A percentage value that’s used to cover expected scrap or other loss during the delivery or production |
7 | Purchase / Procurement Lead time | Days required buying the items from Supplier (Only for P items). MRP uses this in scheduling recommended orders. |
8 | Manufacturing Lead time | The number of working days it takes to manufacture an item, including the time it takes to process paperwork, issue components, Inspect the finished product, and receive it into stock. |
9 | Quality Lead time | The number of working days it takes to inspect a purchased item after it is received |
10 | Subcontracting lead time | This is used for the Subcontracting operations and this time is added based on the SC operation in a ROUTING stage. |
11 | Round off | Decimals and based on this, the QTY ordered and how its kept is controlled (0,1, 2, 3) |
12 | BOM | BOM which is used to explode the RM and WIPs |
13 | Routing ID | To identify the Work center and work loads |
14 | Key Item | If this item is part of a BOM, then we cant produce the FG unless this item is available and is issued. |
15 | The start day of the Week. | |
16 | Working days in a week | This helps to arrive at the total working days in a week |
17 | Duration for Order Release dates | How many days before we have to release the Orders for Production or Purchase` |
18 | MRP Horizon | Material Requirements Planning (MRP)’s MRP horizon is how far to plan forward in time, and is determined by how far ahead demand is known and by the lead times through the manufacturing operation.
For example, we have confirmed SO up to next four months. Question is do we need to consider the Orders for the next four months for the planning or just consider for a month. |
*Send an email to sales@actouch.com to discuss more for any clarifications.
MRP Scheduling / Planning
For materials that are planned according to the Material Requirements Planning (MRP) and Forecast-based planning procedures, the requirement dates in the future are known. Scheduling is always done in Backward schedule mode and if the dates falls short from the Original delivery dates then its Forward Scheduled automatically.
- Backward scheduling – Schedule the dates based on due date to deliver the items and then we plan backwards from that date onwards such that the starting date should be greater than or equal to TODAY. If we don’t meet the deadlines, then we go for Forward Scheduling
- Forward scheduling – In this approach, we start the delivery planning starting from today and we look at when the overall delivery can happen. MRP is designed such that, if the duration to produce an item is less than the delivery dates, then ERP System will automatically changes to Forward Scheduling.
Backward Scheduling Process Flow
The system calculates the following.
- Goods Receipt Time backwards using the Delivery date. This determines the Order finish date (delivery date).
- The in-house production time using the order finish date and thus determines the order start date (backward calculation)
- ERP systems calculates the opening period backwards using the order finish date and thus determines the order opening date.
The ERP System always determines the basic dates for planned orders using Backward Scheduling. ERP systems automatically switches to forward scheduling, if the determined start date lies in the past (<Todays date).
Example
Product Delivery / Requirements date | 25 June (Friday) |
Procurement Duration | 1 day (workday) |
POR Inspection LT | 1 day (workday) |
In-house production time for the material | 6 days (workdays) |
Order Release days | 6 days (workdays) |
Workdays = Monday to Friday, no holidays in between |
Scheduled Dates to release the Order Date
- Requirements date minus Procurement time + Goods Receipt items Inspection Lead Time= order finish date
25 June. (Friday) minus 2 workdays = 23 June (Wednesday)
- Order finish date minus in-house production time= order start date
23 June (Wednesday) minus 6 workdays = 15 June (Tuesday)
- Order start date minus Order Release dates = Order opening date
15 June (Tuesday) minus 6 workdays = 7 June (Monday)
Forward Scheduling
Materials that are planned using Material Requirements Planning (MRP) or Forecast-based planning are switched to forward scheduling if the start date calculated in backward scheduling was in the past. The system determines the date by which the material will be available again, starting from the material shortage date.
In forward scheduling, the opening date is of no significance as the ordering process is started immediately.
Example
Material shortage date | 01 June (Friday) |
Procurement Time | 10 day (workdays) |
Purchase Inspection LT | 1 days (workdays) |
Workdays = Monday to Friday, no bank holiday |
Material shortage date plus Procurement time plus POR Inspection LT = delivery date
01 June (Friday) plus 10 calendar days +1 workday = 14 June (Thursday)
Calculating the Dependent Requirements Date (Little bit of technical words).
As the components and the assemblies are needed for the production of a higher-level planned order, they must be available by the order start date of this higher-level planned order.
If no lead-time offset has been maintained, the system uses the order start date for the source planned order as the dependent requirements date for the components
- Calculating Procurement Quantity (Purchase Quantity) – Material Requirements Planning (MRP) raises the planned orders and these Planned Orders have to be approved. This converts to Purchase indents.
The system determines material shortages for requirement dates in the net requirements calculation. Receipts must now cover these shortage quantities. The ERP System calculates the receipt quantity, which is carried out during the procurement quantity calculation.
Application would use the parameters set in Product Planning module like EOQ, Multiples Of, Scrap %age, Procurement Lead Time, Inspection LT, Round off, Lead time offset parameters
- The system adjusts the determined shortage quantities to match the parameters of the required EOQ and thus determines the order quantity (In case of Purchase)
- If you have made an entry for scrap, the system calculates the scrap quantity and settles this against the total quantity.
- If you have defined a round off value, the system rounds up the lot size and thus calculates the procurement quantity.
Final Quantity = Round off (Required QTY * (1 + scrap %age), 0)
- Calculating Production Date and Time – This generates the WORK ORDER to produce the items as per the demand.
Routing ID for the material is a important and is added into Product Planning Parameters. The production start date and the production finish date, are specified for materials that are produced in-house.
The production dates are determined using the Routing. The system hereby uses the TIME DURATION that are allocated to the material. These Durations are “before production” and “after production” duration and so on.
The ERP system normally executes the time scheduling with backwards scheduling and starts from the agreed order finish date from Sales Order or Forecasting. It only switches to forward scheduling and starts from the order start date, if the duration in routing is substantially shorter than the duration in the material master and the determined production start date is into future than necessary.
- The ERP Software determines the production finish date. Starting from the production finish date, the individual operations of the routing are then scheduled backwards. The starting date of the first operation is the production start date. (Routing is the basis for this)
- The Time duration before production is the number of workdays that are planned as a buffer between the order start date and the production start date. By using this float, delays in material staging do not cause delays in starting production. Additionally, if there are capacity bottlenecks or delays in an incoming sales order, the production dates can be brought forward.
Bill of Materials (BOM)
Materials may appear in several products and in several production levels of a product. The low-level code represents the lowest level of usage of a material within all product structures.
It determines the sequence in which the materials are planned. The system plans materials with the low-level code 0 first and then those with 1 and so on. The lower the low-level code is, the higher the number assigned to the level.
ERP System first calculates the Finished goods (that is manufactured) demand and once the Quantity to manufacture is decided, the BOM for that Finished Goods is exploded and the dependent requirements are determined within MRP Horizon period.
When an MRP is run, the “bill of material” is exploded for every new procurement proposal for an assembly. This helps to control the procurements.
Raw materials and Work In progress items required quantities are determined for all the Assemblies and Finished Goods to manufacture. The ERP system determines the valid BOM that is to be used for the explosion and for determining the dependent requirements.
In summary, MRP is a complex process in an ERP System / MRP System that helps to connect Demand and Supply.
ACTouch is 100% MRP Compliant MRP Software. Register for more details
FAQ on MRP Systems
1. What is Materials Requirement Planning (MRP)?
Materials Requirement Planning (MRP) is a production and inventory management technique that helps businesses ensure they have the right materials available at the right time for production. It involves the systematic planning and scheduling of materials needed for manufacturing, taking into account factors such as lead times, production schedules, and demand forecasts. MRP assists in optimizing inventory levels, minimizing stockouts, and enhancing overall production efficiency.
MRP involves creating a bill of materials (BOM), which outlines the components and quantities required to produce a finished product. By analyzing this BOM along with other factors like production schedules and lead times, MRP software generates plans for purchasing, production, and distribution of materials. The goal is to balance supply and demand, thereby reducing excess inventory and ensuring that production processes run smoothly.
2. What is MRP System?
An MRP system (Materials Requirement Planning system) is a computer-based software tool designed to facilitate the implementation of Materials Requirement Planning. It enables businesses to efficiently manage their materials and inventory by automating tasks such as calculating material requirements, generating purchase orders, and tracking production schedules.
MRP systems use data inputs such as the bill of materials, current inventory levels, lead times, and demand forecasts to create detailed production and purchasing plans. These plans help manufacturers determine when and how much to order, ensuring that materials are available in the right quantities at the right time.
MRP systems offer several benefits, including improved inventory management, reduced stockouts, optimized production scheduling, and enhanced decision-making based on accurate and real-time data.
3. Difference between ERP and MRP Systems?
MRP (Material Requirements Planning) and ERP (Enterprise Resource Planning) systems are related concepts, but they serve different purposes within an organization’s operations.
MRP focuses specifically on the planning and management of materials required for production. It deals with tasks such as creating production schedules, calculating material requirements, and generating purchase orders to maintain adequate inventory levels.
ERP, on the other hand, is a broader system that integrates various business processes, including finance, human resources, sales, and production. ERP systems provide a centralized platform for managing an organization’s entire operations, enabling data sharing and coordination across different departments.
While MRP is a subset of ERP, ERP systems encompass a wider range of functions and often include MRP modules as part of their capabilities. In essence, MRP is concerned primarily with materials and production planning, while ERP encompasses a holistic approach to overall business management.
4. What is ERP MRP Software?
ERP MRP software refers to an integrated solution that combines both Enterprise Resource Planning (ERP) functionalities and Material Requirements Planning (MRP) capabilities. This type of software offers businesses a comprehensive toolset for managing various aspects of their operations, including finance, procurement, human resources, and production planning.
ERP MRP software allows organizations to handle material requirements, production scheduling, inventory management, and other related tasks within a single unified system. This integration enhances data accuracy, reduces redundancies, and streamlines processes by providing a centralized platform for decision-making and resource allocation.
Using ERP MRP software, businesses can align their production and inventory strategies with broader organizational goals, ensuring efficient resource utilization and improved overall performance.
5. What is MRP System Software?
MRP system software is a specialized application designed to implement and execute the principles of Materials Requirement Planning (MRP). This software assists businesses in managing their materials, production schedules, and inventory levels effectively.
MRP system software typically includes features such as:
- Bill of Materials (BOM) Management: Creating and maintaining accurate bills of materials that outline the components required for each product.
- Material Requirements Calculation: Determining the quantities of materials needed based on production schedules and demand forecasts.
- Production Scheduling: Generating production plans and schedules to optimize resource utilization and meet customer demand.
- Purchase Order Generation: Automatically generating purchase orders for required materials based on calculated requirements.
- Inventory Tracking: Monitoring inventory levels, reorder points, and lead times to avoid stockouts and overstocking.
- Reporting and Analytics: Providing insights into material usage, production efficiency, and overall inventory performance.
MRP system software streamlines operations, reduces manual effort, and enhances decision-making by providing accurate and up-to-date information for effective materials management.
6. What is an ERP MRP System?
An ERP MRP system is an integrated software solution that combines the functionalities of both Enterprise Resource Planning (ERP) and Material Requirements Planning (MRP) systems. This type of system offers a comprehensive suite of tools to manage various aspects of an organization’s operations while also addressing the specific needs of materials planning and production scheduling.
An ERP MRP system provides a centralized platform that enables businesses to:
- Manage Materials: Plan, track, and optimize the procurement, storage, and usage of materials required for production.
- Coordinate Resources: Efficiently allocate resources, including labor, machines, and materials, to ensure streamlined production processes.
- Financial Integration: Integrate materials and production data with financial processes to improve cost tracking and budgeting.
- Sales and Demand Forecasting: Combine sales data and demand forecasts to generate accurate material requirements and production schedules.
- Real-time Data: Access real-time information for better decision-making, improved visibility, and enhanced collaboration across departments.
By combining ERP and MRP functionalities, organizations can achieve greater control over their entire supply chain, from raw materials to finished products, resulting in improved efficiency, reduced costs, and enhanced customer satisfaction.
More information, click here
-
Check here the ACTouch’s ERP Features
-
How to implement an ERP Software that’s easy and quick to do?
-
Problems that are faced by an ERP implementation