In the highly competitive manufacturing industry, efficient procurement processes play a crucial role in ensuring smooth operations and sustainable growth. By implementing a robust Procurement / Purchase process, businesses can optimize their supply chain, reduce costs, and enhance overall operational efficiency. ACTouch Cloud ERP Software offers a comprehensive solution to streamline and automate your procurement process, providing numerous benefits for your manufacturing business.
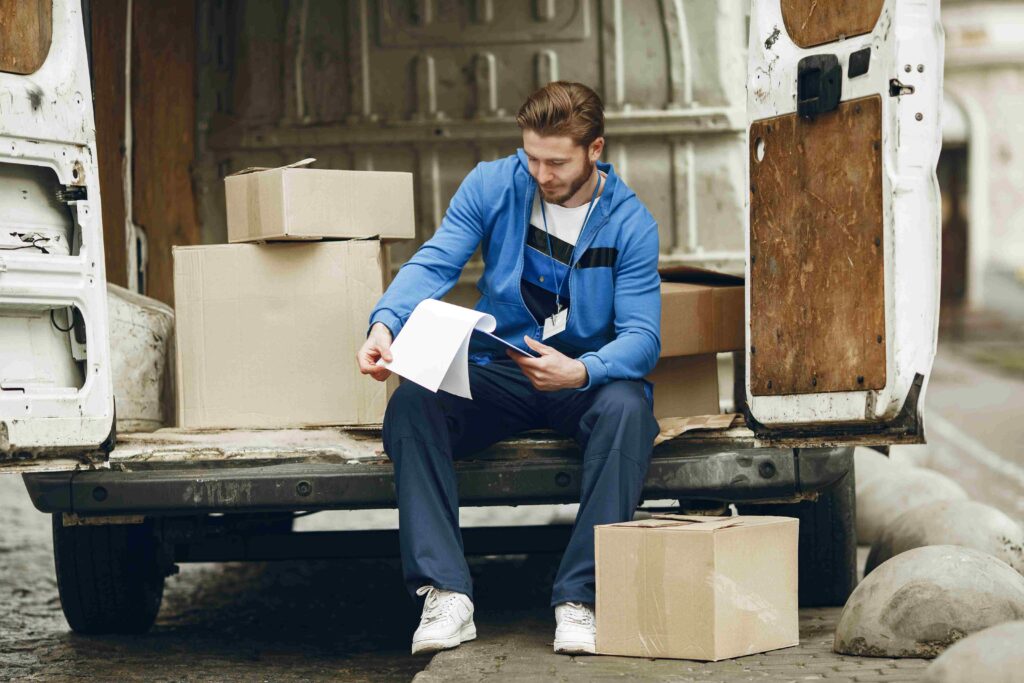
What is a Procurement / Purchase Process?
The procurement process refers to the series of activities involved in acquiring goods and services required for the manufacturing operations of a company. It encompasses various stages, including identifying procurement needs, supplier selection, negotiating contracts, placing purchase orders, receiving and inspecting goods, and managing supplier relationships.
What is the Meaning of Procurement?
Procurement is the strategic approach to sourcing and acquiring goods, services, and resources necessary for the production and operation of a manufacturing company. It involves identifying the right suppliers, negotiating favorable terms, ensuring quality and timely delivery, and managing the overall procurement lifecycle.
Why Procurement is important in Manufacturing Companies?
Procurement plays a crucial role in manufacturing companies for several reasons:
- Reliable Supply of Materials: Manufacturing operations heavily rely on a consistent and reliable supply of raw materials, components, and equipment. Effective procurement ensures the availability of these resources from trusted suppliers, reducing the risk of production delays and ensuring uninterrupted operations.
- Cost Management: Procurement activities, such as negotiation and strategic sourcing, can help manufacturing companies secure competitive pricing and favorable terms with suppliers. By optimizing costs, companies can improve their profit margins and overall financial performance.
- Quality Control: Procurement is responsible for assessing and selecting suppliers based on their quality standards. Through proper vendor evaluation and qualification processes, manufacturing companies can ensure that they source high-quality materials and components, leading to improved product quality and customer satisfaction.
- Supply Chain Efficiency: Procurement plays a vital role in managing the supply chain effectively. By collaborating closely with suppliers, procurement teams can optimize inventory levels, coordinate delivery schedules, and implement just-in-time practices. These efforts streamline the supply chain, minimize stockouts, reduce inventory carrying costs, and enhance overall operational efficiency.
- Innovation and Technology Integration: Procurement is not only focused on sourcing materials but also on identifying innovative suppliers and fostering collaboration for continuous improvement. By keeping up with industry trends and exploring new technologies, procurement can drive innovation within the manufacturing company, leading to enhanced product offerings and competitive advantages.
- Risk Management: Procurement teams are responsible for assessing and mitigating risks associated with the supply chain. They monitor supplier performance, track market trends, and develop contingency plans to address potential disruptions such as supplier failures, price fluctuations, or changes in market conditions. This proactive approach helps manufacturing companies mitigate risks and maintain business continuity.
- Sustainable and Ethical Practices: Procurement can contribute to a manufacturing company’s commitment to sustainability and ethical practices. By evaluating suppliers’ environmental and social responsibility, companies can align their procurement processes with sustainable goals, such as sourcing from eco-friendly suppliers or those with fair labor practices.
Procurement is important in manufacturing companies because it ensures a reliable supply of materials, manages costs, enhances product quality, improves supply chain efficiency, drives innovation, mitigates risks, and promotes sustainability. Effective procurement practices contribute to the overall success and competitiveness of manufacturing businesses.
Difference Between Procurement and Purchase Process
While procurement and purchasing are often used interchangeably, they have distinct meanings. Procurement refers to the broader process of acquiring goods and services, including activities such as supplier selection, contract negotiation, and supplier relationship management. On the other hand, Purchasing specifically refers to the act of placing orders and acquiring goods from suppliers based on predefined specifications and pricing.
What are the Types of Procurement?
There are several types of procurement methods commonly used in manufacturing companies. The specific procurement method chosen depends on various factors such as the nature of the goods or services being procured, the level of complexity, the desired level of control, and the organization’s strategic objectives. Here are some common types of procurement:
Traditional Procurement
This method involves a traditional approach of identifying suppliers, requesting quotes or proposals, negotiating contracts, and making purchases. It typically follows a structured and formal process, involving multiple bids and evaluation criteria.
Strategic Sourcing
Strategic sourcing focuses on developing long-term relationships with suppliers to optimize the procurement process. It involves analyzing the supply market, identifying key suppliers, and negotiating favorable terms and conditions. This approach emphasizes a collaborative partnership to drive innovation, cost savings, and supply chain improvements.
Single-Source Procurement
Single-source procurement involves sourcing from a single supplier for specific goods or services. This approach is chosen when there is a unique or specialized product, a strong supplier relationship, or a need for consistency in quality or specifications.
Framework Agreements
Framework agreements are long-term contracts with pre-qualified suppliers. These agreements establish terms and conditions for future purchases within a specific period. This method streamlines the procurement process by eliminating the need for repeated negotiations and allows for flexibility in making subsequent purchases.
Outsourced Procurement
Some companies choose to outsource their procurement functions to specialized third-party organizations. This allows the company to leverage the expertise and resources of the procurement service provider, reducing costs and improving efficiency.
Just-in-Time (JIT) Procurement
JIT procurement involves sourcing and delivering materials or components at the exact time they are needed in the production process. This approach minimizes inventory holding costs, reduces waste, and improves operational efficiency.
E-Procurement
E-Procurement refers to the use of electronic platforms and technology to streamline the procurement process. It includes online bidding, e-auctions, vendor portals, and electronic purchase order systems. E-Procurement simplifies the sourcing process, improves transparency, and enhances collaboration between buyers and suppliers.
It’s important for manufacturing companies to assess their specific requirements and choose the procurement method that aligns with their goals, operational needs, and strategic objectives. The selection of the appropriate procurement method can significantly impact the efficiency, cost-effectiveness, and overall success of the procurement process.
What is a Vendor Management System?
A vendor management system (VMS) is a software solution that enables businesses to effectively manage their relationships with suppliers and vendors. It streamlines the vendor selection process, automates purchase order management, tracks supplier performance, and facilitates communication and collaboration between the company and its vendors. ACTouch Cloud ERP Software provides a robust VMS module that helps streamline vendor management and improve procurement efficiency.
Functions of the Purchase Department:
The purchase department plays a vital role in the procurement process of a manufacturing company. Its key functions include:
- Identifying procurement needs and requirements based on production plans and inventory levels.
- Sourcing and selecting reliable suppliers who can provide high-quality goods and services.
- Negotiating favorable terms and conditions, including pricing, delivery schedules, and payment terms.
- Managing purchase orders and ensuring timely delivery of materials to support production schedules.
- Conducting supplier performance evaluations and maintaining healthy supplier relationships.
- Collaborating with other departments, such as production, finance, and quality control, to ensure seamless operations and adherence to procurement guidelines.
8 Steps of Procurement Life Cycle
The procurement life cycle represents the entire journey of a procurement process, from the identification of needs to supplier evaluation and contract management. It typically consists of the following stages:
- Need Identification: Assessing the organization’s requirements and determining the need for procurement.
- Supplier Selection: Identifying potential suppliers, evaluating their capabilities, and selecting the most suitable ones.
- Contract Negotiation: Negotiating terms and conditions, pricing, and other contractual details with selected suppliers.
- Purchase Order Placement: Generating and issuing purchase orders to the chosen suppliers.
- Receipt and Inspection: Receiving and inspecting the goods or services to ensure quality and adherence to specifications.
- Invoicing and Payment: Processing supplier invoices and making timely payments as per agreed-upon terms.
- Supplier Performance Evaluation: Assessing supplier performance based on factors such as quality, delivery, and responsiveness.
- Contract Renewal or Termination: Reviewing and renewing contracts with reliable suppliers or terminating contracts with underperforming ones.
How Procurement and Finance are connected?
Procurement and finance are closely connected within an organization. The procurement function is responsible for acquiring goods and services necessary for the organization’s operations, while the finance function manages the financial aspects of the organization. Here’s how procurement and finance are interconnected:
- Budgeting and Planning: The finance department and procurement department collaborate in the budgeting and planning process. The procurement team provides insights into the anticipated procurement needs and associated costs, which helps the finance team allocate appropriate budgets for procurement activities.
- Cost Management: Procurement plays a vital role in cost management, as it involves negotiating favorable pricing and terms with suppliers. The finance team closely monitors and analyzes the procurement spend to ensure it aligns with the budgeted amounts and overall financial goals. They work together to identify cost-saving opportunities, optimize procurement processes, and track expenses related to procurement activities.
- Financial Reporting: Procurement activities impact financial reporting, as they involve the purchase of goods and services, which in turn affect the organization’s financial statements. The finance department incorporates the procurement data into financial reports, such as the income statement and balance sheet, to accurately reflect the organization’s financial position and performance.
- Payment Processing: Finance oversees the payment processing function, which includes verifying invoices received from suppliers, matching them with purchase orders and contracts, and ensuring timely and accurate payment. Procurement provides the necessary documentation and information to facilitate smooth payment processing.
- Cash Flow Management: Effective procurement practices can have a significant impact on cash flow management. By optimizing procurement processes, negotiating favorable payment terms, and managing supplier relationships, the procurement department contributes to maintaining healthy cash flow levels. The finance team closely monitors cash flow and works with procurement to align payment schedules with available funds.
- Financial Compliance: Procurement activities must comply with financial regulations, internal controls, and company policies. The finance department ensures that procurement processes adhere to these guidelines to mitigate financial risks, maintain transparency, and uphold ethical practices.
FAQ on Procurement Process
What is procurement?
Procurement refers to the process of acquiring goods, services, or resources necessary for a business’s operations.
What are the key steps in the procurement process?
The procurement process typically involves identifying procurement needs, supplier selection, negotiation, contract management, purchase order placement, receipt and inspection of goods, and supplier relationship management.
How can procurement benefit a manufacturing company?
Effective procurement can help manufacturing companies optimize their supply chain, reduce costs, improve quality control, ensure timely delivery of materials, and foster strong supplier relationships.
What is strategic sourcing in procurement?
Strategic sourcing is a proactive approach to procurement that focuses on identifying the best suppliers, negotiating favorable terms, and managing supplier relationships to achieve cost savings, quality improvement, and supply chain efficiency.
How is procurement different from purchasing?
Procurement encompasses the entire process of acquiring goods and services, including supplier selection, negotiation, and relationship management. Purchasing specifically refers to the act of placing orders and acquiring goods from selected suppliers.
What is the role of a procurement manager?
A procurement manager is responsible for overseeing the procurement process, managing supplier relationships, ensuring compliance with procurement policies, negotiating contracts, and optimizing procurement strategies to meet the company’s needs.
What is e-procurement?
E-procurement, or electronic procurement, refers to the use of digital platforms and technologies to automate and streamline the procurement process. It includes activities such as online supplier catalogs, electronic purchase orders, and online bidding systems.
How can procurement contribute to cost savings?
By effectively managing supplier relationships, negotiating favorable pricing and terms, and optimizing procurement strategies, companies can achieve cost savings through bulk purchasing, reduced inventory holding costs, and improved efficiency in the supply chain.
What is a request for proposal (RFP) in procurement?
An RFP is a document issued by a company to potential suppliers, inviting them to submit proposals outlining their capabilities, pricing, and other relevant information. It helps the company evaluate suppliers and make informed procurement decisions.
Remember to customize and expand upon these answers to align with your specific requirements and the features of your ACTouch Cloud ERP software.