Finding ways to optimise operations and improve efficiency is crucial for Manufacturing / Trading Business success. One effective strategy that can significantly impact your business’s profitability and inventory management is implementing a Minimum Order Quantity (MOQ) policy. In this article, we will explore what MOQ is, it’s impact on inventory, the benefits it offers, potential drawbacks, and how to calculate the ideal MOQ for your business.
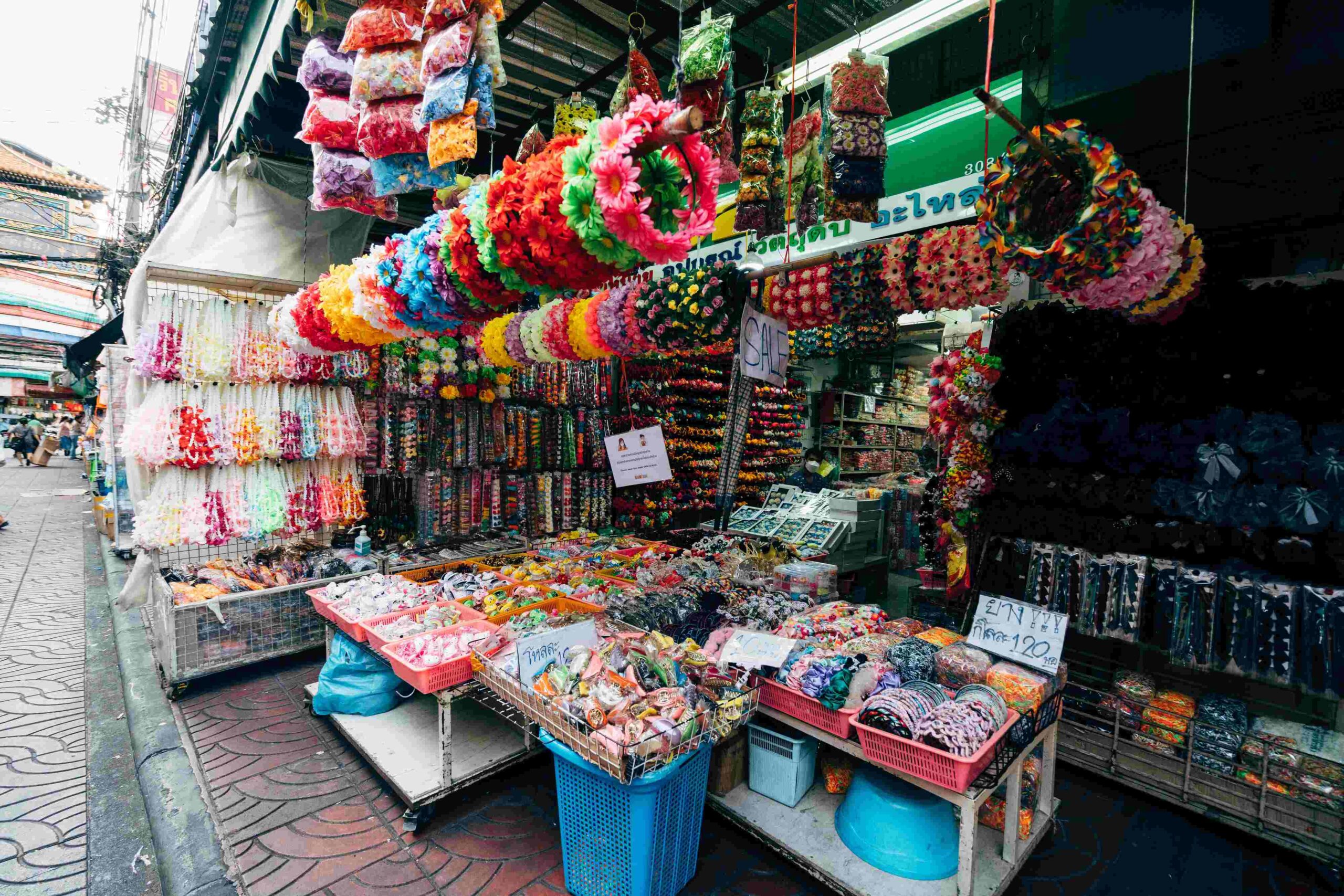
What is Minimum Order Quantity (MOQ)?
MOQ refers to the smallest quantity of a product that a manufacturer or supplier is willing to produce or sell in a single order. It sets a threshold that customers must meet to place an order. The MOQ can be defined based on various factors such as production capabilities, economies of scale, supplier constraints, and customer demand.
Examples of Minimum Order Quantity:
- Clothing Manufacturer: A clothing manufacturer may have an MOQ of 100 pieces per style for custom orders.
- Electronics Supplier: An electronics supplier may set an MOQ of 500 units for a specific component due to manufacturing setup costs.
How does Minimum Order Quantity Impact Inventory?
Implementing an MOQ policy can have a significant impact on inventory management:
- Efficient Stock Management: MOQ helps prevent stockouts by ensuring a minimum level of demand for each product. It enables manufacturers to plan their production and procurement processes effectively.
- Reduced Inventory Holding Costs: By setting MOQs, businesses can avoid excess inventory and associated costs such as storage, insurance, and obsolescence.
- Streamlined Supply Chain: MOQs allow for better coordination with suppliers and optimize the flow of materials, ensuring timely production and delivery of products.
Benefits of Minimum Order Quantity:
a) Cost Savings: MOQs often lead to volume discounts and lower unit costs, enabling businesses to improve their profit margins.
b) Production Efficiency: By consolidating orders into larger quantities, manufacturers can optimize their production processes, reduce setup time, and achieve economies of scale.
c) Improved Customer Satisfaction: MOQs can ensure consistent product availability, reduce lead times, and enable timely order fulfillment, enhancing customer satisfaction and loyalty.
The Disadvantages of Minimum Order Quantity:
a) Higher Initial Investment: MOQs may require businesses to commit to larger order quantities, resulting in increased upfront costs.
b) Inventory Risk: Setting MOQs too high may lead to excess inventory if demand fluctuates or product preferences change.
c) Restricted Flexibility: MOQs can limit customization options and restrict small-scale buyers from accessing certain products.
How to Calculate Minimum Order Quantity:
Calculating the Minimum Order Quantity (MOQ) involves considering various factors to determine the optimal quantity that should be ordered to meet specific requirements. While the exact calculation may vary depending on the specific context and industry, the following steps provide a general approach to calculating the MOQ:
- Analyse Demand: Begin by analyzing the historical demand patterns for the product. Consider factors such as sales data, customer orders, and market trends. This analysis will help you understand the average demand for the product within a specific timeframe.
- Consider Lead Time: Determine the lead time required to fulfill an order, which includes the time taken for production, procurement, and delivery. Consider any seasonal or cyclical variations that may impact lead times.
- Evaluate Supplier Constraints: Engage in discussions with your suppliers to understand their production capabilities, constraints, and minimum requirements for production runs. Suppliers may have their own MOQs based on production efficiency, setup costs, or material availability.
- Calculate Safety Stock: Safety stock is the additional inventory maintained to account for unexpected fluctuations in demand or lead time. Calculate the required safety stock based on factors such as desired service level, historical demand variability, and lead time variability.
- Consider Economic Factors: Assess the impact of economic factors on ordering quantities. Consider factors such as price breaks, discounts, freight costs, and storage costs. Sometimes, it may be more cost-effective to order a slightly higher quantity to take advantage of better pricing or reduced shipping costs.
- Evaluate Storage Capacity: Assess your storage capacity and ensure that the calculated MOQ aligns with your storage capabilities. Avoid overstocking if it exceeds your available space, which can lead to additional storage costs and operational challenges. Please arrive at the Inventory Carrying Costs too.
- Balancing Factors: Finally, evaluate and balance all the factors mentioned above to arrive at an optimal MOQ that aligns with your business goals, customer requirements, and supply chain efficiency. This may involve iterative calculations and adjustments based on changing circumstances.
Best Practices for Calculating Minimum Quantity Order:
- Collaborate with suppliers: Engage in open communication with suppliers to understand their constraints, negotiate favorable terms, and explore possibilities for reducing MOQs.
- Consider customer requirements: Take into account the preferences and needs of your customers to ensure that the MOQ aligns with their expectations and buying behavior.
- Monitor and refine: Continuously monitor and analyze demand patterns, lead times, and other factors influencing the MOQ. Regularly review and refine the calculations to adapt to changing market conditions and optimize your ordering quantities.
By implementing these best practices and utilizing ACTouch Cloud ERP Software, you can streamline the calculation and management of your MOQs. The software can provide real-time insights into demand patterns, inventory levels, and supplier capabilities, allowing you to make data-driven decisions and optimize your ordering processes for improved efficiency and cost-effectiveness.
Find the MOQ with the help of our Free MOQ Calculator Now.
Difference between Economic Order Quantity (EOQ) and MOQ
Economic Order Quantity (EOQ) and Minimum Order Quantity (MOQ) are two inventory management concepts that serve different purposes in the manufacturing industry. While both are related to order quantities, they have distinct characteristics and applications. Let’s explore the difference between EOQ and MOQ:
Economic Order Quantity (EOQ)
EOQ is a calculation that helps determine the optimal order quantity for a specific item by balancing inventory holding costs and ordering costs. The goal of EOQ is to minimize the total cost associated with inventory management. The following factors are considered in the EOQ calculation:
- Demand: The average demand for the item over a specific period.
- Ordering Cost: The cost incurred each time an order is placed, including administrative expenses, processing fees, and transportation costs.
- Holding Cost: The cost of carrying inventory, including storage fees, insurance, and obsolescence.
The EOQ formula takes into account these factors and calculates the order quantity that minimizes the total cost of inventory management. The objective is to strike a balance between holding too much inventory (resulting in increased holding costs) and ordering too frequently (resulting in increased ordering costs).
Minimum Quantity Quantity
MOQ, on the other hand, represents the minimum quantity of a product that a manufacturer or supplier is willing to produce or sell in a single order. It is typically determined based on factors such as production capabilities, supplier constraints, economies of scale, and customer demand. MOQ sets a threshold that customers must meet to place an order.
The primary purpose of MOQ is to ensure efficient production and distribution. By setting a minimum order quantity, manufacturers can optimize their production processes, reduce setup time, and achieve economies of scale. MOQ also helps prevent stockouts by ensuring a minimum level of demand for each product.
In summary, the key differences between EOQ and MOQ are as follows:
- EOQ focuses on determining the optimal order quantity to minimize total inventory management costs.
- MOQ represents the minimum quantity required for a single order and aims to optimize production and distribution processes.
- EOQ considers both holding costs and ordering costs, while MOQ is primarily influenced by production capabilities, economies of scale, and customer demand.
Both EOQ and MOQ are valuable tools in inventory management. Implementing an effective EOQ strategy helps businesses balance costs, while adhering to MOQ requirements enables manufacturers to optimise their production processes and achieve economies of scale. Minimum Order Quantity is a powerful tool that can enhance your manufacturing operations by improving inventory management, reducing costs, and optimizing production processes. By implementing an effective MOQ strategy, you can streamline your supply chain, satisfy customer demands, and boost profitability.
FAQ on MOQ’s
below are the FAQ’s based on Google search questions on MOQ’s
1. What is Minimum Order Quantity (MOQ)?
Minimum Order Quantity refers to the lowest quantity of a product that a supplier or manufacturer is willing to produce or sell in a single order.
2. Why do suppliers have MOQs?
Suppliers often have MOQs to ensure that the production or sale of a product is financially viable. MOQs help cover setup costs, ensure efficient production, and maintain profitability.
3. How are MOQs Calculated?
MOQ is determined based on various factors, including production efficiency, material availability, setup costs, storage capacity, and market demand. Suppliers calculate MOQs to optimize their operations and meet customer requirements.
4. What are the benefits of MOQ?
MOQ offers several benefits, such as:
- Ensuring cost-effective production or procurement by optimizing resources.
- Streamlining supply chain operations and reducing handling costs.
- Encouraging bulk purchases and providing better pricing or discounts.
- Reducing inventory holding costs and minimizing stockouts.
5. What are the disadvantages of MOQ?
While MOQs have their advantages, some potential drawbacks include:
- Higher upfront costs for customers when ordering in large quantities.
- Increased inventory levels, which can tie up capital and require additional storage space.
- Limited flexibility for customers who have varying or unpredictable demand patterns.
- Potential wastage or obsolescence if demand decreases or product specifications change.
6. Can MOQs be negotiated?
Yes, MOQs can often be negotiated with suppliers, especially in cases where you have a long-standing relationship, high purchase volumes, or when demand is uncertain. It’s important to have open communication and explore possibilities for adjusting MOQs based on mutual benefits.
7. How can I manage MOQs effectively?
To manage MOQs effectively, consider the following:
- Analyze customer demand patterns to forecast requirements accurately.
- Maintain good relationships with suppliers and negotiate favorable terms.
- Explore options for consolidating orders or collaborating with other businesses to meet MOQs.
- Utilize inventory management software, like ACTouch Cloud ERP, to monitor stock levels, track customer orders, and optimize procurement processes.
8. Can MOQs change over time?
Yes, MOQs can change over time based on factors such as market conditions, supplier capabilities, or changes in your own business requirements. It’s essential to regularly evaluate and adjust MOQs to align with your evolving needs and maintain competitiveness.
Remember, these FAQs and their answers can be used as a starting point to provide valuable information to potential customers about the concept of Minimum Order Quantity and its significance.